In the intricate realm of metalwork, mastering diverse techniques is paramount. Yet, many grapple with distinguishing between metal stamping and metal fabrication—two core methods. For industry aficionados and professionals alike, understanding this distinction is crucial for optimal outcomes.
Metal stamping is the art of employing dies to morph flat metal sheets into desired shapes. On the flip side, metal fabrication stands as an umbrella term, covering a spectrum of techniques aimed at designing, assembling, and crafting metal structures.
Venture further as we delve into the depths of metal stamping and metal fabrication, unraveling their complexities, applications, and the unique advantages each brings to the table.

Understanding Metal Stamping
Definition and Basics of Metal Stamping
Metal stamping is a specialized manufacturing process where sheets of metal, typically in coil form, are fed into a press that houses a tool and die surface. This tool and die surface uses force to shape and cut the metal into the desired form, creating objects or parts used in various products and industries.
Common Applications and Industries that Rely on Stamping
Metal stamping is ubiquitous in its application. From the automotive industry, where it’s used to create car parts and components, to electronics, where tiny metal parts are stamped for devices and appliances. Other sectors include aerospace, medical devices, consumer electronics, and even jewelry. The versatility of metal stamping means it’s a preferred method for producing high volumes of complex parts with precision.
Benefits of Opting for Metal Stamping:
There are several advantages to choosing metal stamping:
- Efficiency: Ideal for producing large quantities due to its high-speed production capability.
- Accuracy: Advanced stamping techniques ensure consistent and precise results, reducing the margin of error.
- Cost-Effective: Given its suitability for mass production, unit costs are often lower than other manufacturing methods.
- Versatility: Capable of producing a wide range of shapes and designs, from simple to intricate.
- Durability: Stamped parts often exhibit enhanced strength and durability, especially when specific metals or alloys are used.
By understanding the essence and advantages of metal stamping, industries can harness its potential for a myriad of applications, ensuring quality and efficiency in their products.

Delving into Metal Fabrication
What Does Metal Fabrication Entail?
Metal fabrication is a multifaceted process that involves manipulating metal materials to create a product. It encompasses everything from cutting, bending, and assembling metal to create finished structures or products. Unlike metal stamping, which primarily reshapes metal, fabrication often involves joining multiple pieces or even different metals together.
Different Techniques Under the Umbrella of Fabrication
There are several techniques within the realm of metal fabrication, including:
- Cutting: Using tools or machinery like lasers, plasma torches, or water jets to slice metal.
- Bending: Modifying the shape of metal using manual or automated hammers and press brakes.
- Welding: Joining separate metal pieces together using heat.
- Machining: Removing parts of the metal to shape it, typically using lathes or milling machines.
- Punching: Creating holes in metal using a punch press.
- Shearing: Making long cuts on metal sheets.
- Stamping: Yes, metal stamping can also be a part of the fabrication process, especially when specific shapes are needed on a fabricated piece.
- Assembly: Joining various metal components together, often using techniques like welding, riveting, or threaded fasteners.
Industries Where Metal Fabrication Plays a Pivotal Role
Metal fabrication’s versatility means it’s integral to numerous industries. Some of the primary ones include:
- Construction: For creating structural components, beams, and frameworks.
- Automotive: In producing parts, frames, and even intricate components for vehicles.
- Aerospace: Crafting parts for aircraft and space vehicles.
- Energy: Especially in the oil and gas sector, where pipelines and platforms are needed.
- Electronics: For making casings, components, and more.
- Agriculture: In the production of machinery and tools.
- Maritime: Building parts for ships, submarines, and other marine vehicles.
Metal fabrication, with its array of techniques, is a cornerstone of modern manufacturing, serving a plethora of industries and ensuring they function seamlessly.
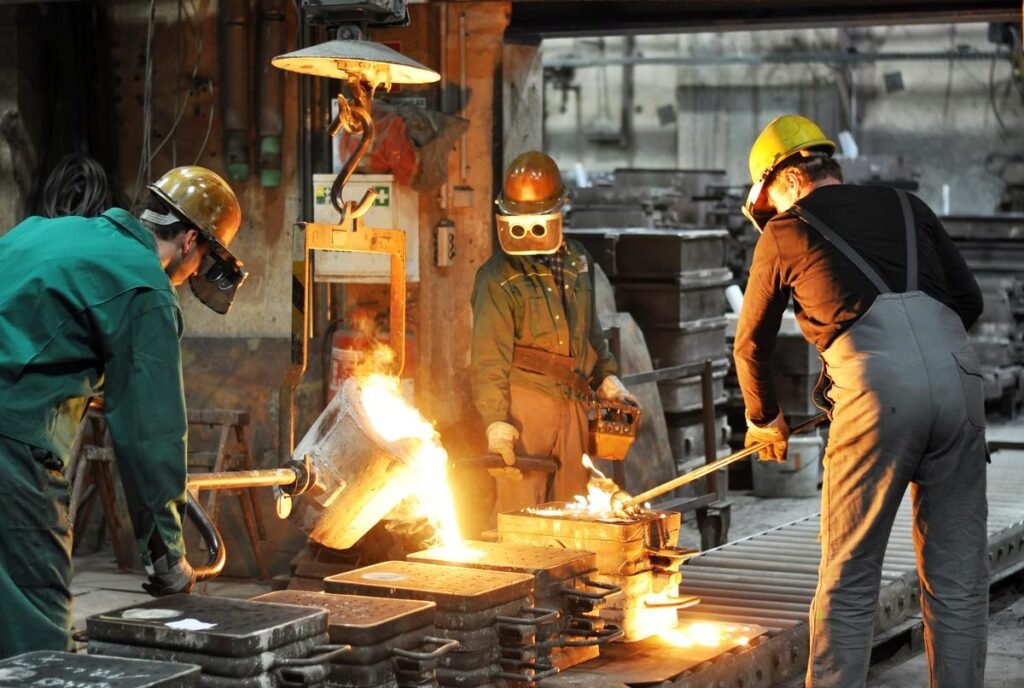
Key Differences Between Stamping and Fabrication
Comparison of Techniques, Tools, and Processes:
- Metal Stamping:
- Techniques: Primarily involves pressing or punching using dies to create shapes, patterns, or holes.
- Tools: Utilizes stamping presses, dies, and punch sets.
- Processes: Often a single-step process where a machine produces parts at high speeds.
- Metal Fabrication:
- Techniques: Encompasses a range of methods from cutting, bending, welding, to assembling.
- Tools: Incorporates a diverse set of tools like lasers, plasma torches, welding machines, lathes, and milling machines.
- Processes: Typically multi-step, involving various techniques to achieve the final product.
Cost Implications of Both Methods:
- Metal Stamping:
- Initial Costs: Setting up for metal stamping can be expensive due to the need for custom dies and tooling.
- Per Unit Cost: Highly cost-effective for large-scale production runs as the same die can produce vast quantities rapidly.
- Metal Fabrication:
- Initial Costs: Generally lower than stamping, especially for custom, low-volume projects.
- Per Unit Cost: Might be higher than stamping for large quantities, but offers flexibility for bespoke projects.
Suitability Based on Project Requirements:
- Metal Stamping:
- Best For: High-volume production where thousands or millions of identical parts are needed.
- Limitations: Less flexible for custom, small-batch projects due to the high initial setup cost.
- Metal Fabrication:
- Best For: Custom projects, prototypes, or low to medium volume production. Ideal for projects requiring a variety of metals and techniques.
- Limitations: Might not be as cost-effective as stamping for very high-volume runs.
In essence, while both metal stamping and fabrication are invaluable in the manufacturing world, their suitability varies. It’s essential to assess the project’s scale, budget, and specificity to determine the best approach.

Advancements in Metalwork
a. Modern Technologies Enhancing Both Stamping and Fabrication:
- 3D Printing: While traditionally associated with plastics, metal 3D printing is on the rise, allowing for rapid prototyping and even production of complex metal parts that would be challenging with traditional methods.
- Laser Cutting and Engraving: High-precision lasers can cut intricate designs into metal with extreme accuracy, and they’re becoming more affordable and widespread.
- High-Speed CNC Machining: Computer Numerical Control (CNC) machines can produce metal parts at incredible speeds and with high precision, revolutionizing both stamping and fabrication processes.
- Electromagnetic Forming: A process that uses magnetic fields to shape metal, allowing for designs that were previously impossible or impractical.
- Robotic Welding: Ensures consistent, high-quality welds and can operate at speeds unattainable by human welders.
b. The Role of Automation and Computer-Aided Design (CAD):
- Automation in Production: Automated machinery in metalwork, especially in stamping, ensures consistent quality, faster production rates, and reduced labor costs. Robots and automated systems can handle repetitive tasks, from welding to bending, with precision.
- Computer-Aided Design (CAD): CAD software has transformed the design phase in metalwork. Designers can create detailed 3D models of parts, test them in virtual environments, and make modifications before any actual manufacturing begins. This reduces errors, saves time, and ensures a better final product.
- Integration of CAD with Machinery: Modern machines can directly interpret CAD designs, allowing for seamless transition from design to production. This integration reduces the chances of human error and streamlines the manufacturing process.
- Predictive Maintenance: With the integration of IoT (Internet of Things) sensors, machines can predict when they might fail or need maintenance, reducing downtime and increasing efficiency.
The advancements in metalwork, driven by technology and innovation, are reshaping the industry. The fusion of traditional techniques with modern technology ensures higher precision, efficiency, and opens the door to new possibilities in metal manufacturing.

Making the Right Choice for Your Project
Factors to Consider When Choosing Between Stamping and Fabrication:
- Volume of Production: If you’re looking at producing large quantities of a specific part, stamping might be more cost-effective. For smaller batches or custom projects, fabrication offers more flexibility.
- Complexity of Design: For intricate designs that require multiple techniques or materials, fabrication might be the better choice. Stamping is ideal for simpler designs that need to be replicated many times.
- Budget Constraints: While stamping can have higher initial setup costs due to custom dies, it becomes cost-effective in high volumes. Fabrication might have lower startup costs but can be pricier per unit for large batches.
- Lead Time: If you’re pressed for time, consider the setup period. Fabrication can often begin sooner, while stamping might require additional time for die preparation.
- Material Used: Some materials are better suited for stamping, while others are more compatible with fabrication techniques. Research or consult with experts on the best method for your chosen material.
- Tolerance and Precision: If your project requires extremely tight tolerances, certain fabrication techniques like CNC machining or laser cutting might be preferable.
Expert Insights and Recommendations:
- Consult with Manufacturers: Before finalizing a method, it’s wise to consult with manufacturers who have expertise in both stamping and fabrication. They can provide insights based on previous projects and their equipment capabilities.
- Stay Updated with Industry Trends: The metalworking industry is evolving rapidly. New techniques and technologies can offer better solutions, so it’s beneficial to stay informed.
- Consider Future Needs: If your project might scale up in the future, consider how easy it will be to transition from one method to another. For instance, starting with fabrication for prototypes and switching to stamping for mass production.
- Quality Over Cost: While budget constraints are real, prioritizing quality will pay off in the long run. A slightly more expensive method that offers better results might save costs in terms of repairs, replacements, or customer satisfaction down the line.
In conclusion, the decision between metal stamping and fabrication hinges on the specifics of your project and long-term goals. By weighing the factors and seeking expert advice, you can ensure that your project is executed efficiently and to the highest standards.

Conclusion
Metal stamping and fabrication, each with its distinct advantages, serve as pillars in the metalworking realm. While stamping offers precision in high volumes, fabrication shines in versatility and customization. As you embark on your next project, take a moment to assess its nuances and seek expert guidance to chart the best course forward.