Metal drawing is quite a generalized metal forming process for creating hollow parts of various dimensions, including depth and size. However, two typical processes, deep and shallow drawing, are the most utilized. The deep drawing vs shallow drawing debate is intriguing since these two techniques are only slightly nuanced. They utilize similar metal forming principles, and virtually every aspect involved is indifferent. Regardless, it helps to understand these variations and what each process can result in. This article takes into the deep and shallow metal drawing comparison, explaining the intricate details observed in each.
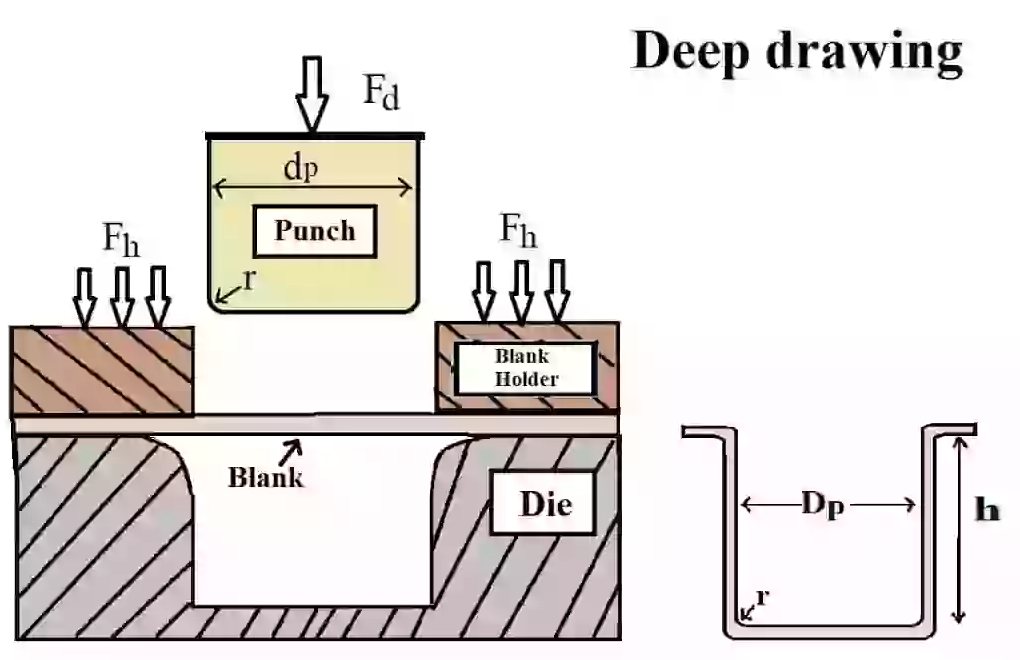
Deep Drawing and Shallow Drawing: What are They?
Metal drawing is a tensile process classified under metal forming and deformation. The extent of deformation, therefore, determines whether you’ll categorize it under deep or shallow drawing. Shallow drawing occurs when the depth of the draw is less than the tiniest dimension of the opening. However, it’s considered a deep drawing if it goes more profoundly. The process qualifies as deep drawing if the height-to-diameter ratio exceeds 0.5. conversely, we can take it as a shallow drawing if this ratio is less.
How do Deep Drawing and Shallow Drawing Happen?
Both processes use similar metal-forming apparatus and materials, including blanks, dies, and blank holders. However, the punch and force vary, and it’s the thin line between telling deep drawing and shallow drawing apart. Shallow drawing uses less drawing force, and although the stretching limit is usually already predetermined, it’s not incredibly profound as deep drawing. Considerations must occur for both processes to be successful and eliminate the potential fault.
Considerations in Metal Drawing Processes
The following considerations must ensure a seamless process and flawless results.

Calculating sheet metal blank size
- Calculating the blank’s surface area using the formula πRb2
- Calculating the cup’s surface area (finished part) using the formula πRf2 = 2πRF Hf
- Keeping blank’s and cup’s (finished part) surface areas equal by equating the two formulas.
πRb2 = πRf2 = 2πRF Hf
RB = √ Rf (Rf = 2 Hf)
Note: Rb = Blank’s radius
Rf = Finished part’s radius
Hf = Finished part’s height
Here’s an example to help you understand better metal drawing size calculations.
Calculate the number of drawing operations and the blank diameter for deep drawing a cup with the finished part’s dimensions: 50 mm diameter and 60 mm cup depth.
Using the formula πRb2 = πRf2 = 2πRF Hf
= √24 (25 + 2 x 60)
= 60.2 mm
doubling the radius, we get the blank’s diameter
60.2 mm x 2 = 120.4
Calculating the draw reduction ratio
The deep draw ratio (DDR) helps determine the number of draw operations using the formula:
DDR = Blank diameter – needed punch diameter
Blank diameter
Assuming that we want to shallow-draw a blank sheet, and the DDR is 0.5, the product of this value and the blank diameter should give us the number of drawing operations.
Using our example above (and assuming the punch diameter is half the size of the blank diameter), the number of operations should be:
DRR x Blank Diameter = (Blank diameter – Punch diameter)
= 0.5 x 120.4 = 120.4 – Punch Diameter
The Punch diameter should be 60.2, coincidentally representing our finished part’s height (Hf). In this case, we only need a single draw operation.
Calculating the maximum deep drawing force
The maximum drawing force needed is as essential as other aspects of creating the projected finished part with pinpoint accuracy. The formula that metal drawing operations use to calculate this force is:
Maximum drawing force = π (d + t) x t x UTS
Where
t = The blank thickness
d = The punch diameter and,
UTS = The ultimate tensile strength for the sheet metal material
What Defines Shallow Drawing and Deep Drawing Operations?
The draw reduction ratio is essentially the thin line separating the two similar yet varied operations. Deep drawing operations use DDR more than 0.5. however, deep drawing operations can have a higher ratio, starting from 0.5 and beyond. Most shallow drawing products have tinier depths than metal saucers and shallow basins. Usually, the depth of the drawing is less compared to the tiniest dimensions of the hole.
However, deep-drawn metal parts are more profound in-depth than the tiniest dimension of the hole. Typical deep-drawn products include electric kettle cylinders and car piston cylinders having more profound depths.
Which Between Deep Drawing and Shallow Drawing is Sought-After?
Deep-drawn metal parts are the most popular since a vast array of manufacturing companies, including automotive and aerospace, utilize them. However, shallow-drawn parts are still practically valuable for many industries, including electronics and building hardware. Both parts are equally helpful in their regard and capacity, forming structural components in machinery architecture and electronics chasses.
The industrial revolution craze saw the use of drawn metal demand soaring, and it’s since remained that way for quite a long time. The demand has been increasing by the day, and these metal parts could be mainstream in many years. Regardless of the type, whether shallow or deep or widespread, both metal drawing processes have proven essential in manufacturing.
Essential Deep Drawing and Shallow Drawing Elements to Consider
While the deep and shallow drawing calculations must click correctly, other elements must come into play for successful operation. The blank needs to measure up to a few set elements, but the die and the entire drawing apparatus must be in perfect shape. The crucial element to consider in deep and shallow stamping operations include the following.
Availability of Lubricants
Lubricants minimize friction that can be more compromising in metal drawing operations. Scratching and denting are possible if no friction reduction mechanisms exist. So it’s typical for most metal drawing operations to use soap-based lubricants, emulsions, and other unique drawing oils. Besides minimizing friction, these lubricants’ propensity to absorb generated heat makes it easy to maintain at the most required levels.
Die Temperature
Die temperatures during metal stamping operations determine whether or not the process will achieve the efficiency and dimensional accuracy of the finished part. Mainly, friction is the primary culprit for high die temperature, impacting the physical capacity of blanks to handle the stress and tensile forces. Some blank materials may become more brittle when exposed to die heat, while others can stretch more than intended due to an increased flow.
Punch Speed
While calculating the punch force is easy, the speed also needs to measure correctly to minimize possible wrinkling and tearing. It’s wiser to ensure that the metal seamlessly flows as the upper blanking die administers the punch. And that’s possible if the punching speed doesn’t subject the metal blank to unnecessary jerks and pressure, causing wrinkling and tearing.
Possible Defects in Deep Drawing and Shallow Drawing
Like every metal forming operation, deep and shallow drawing processes are subject to fault. While these defects are expected, it’s ideal to minimize them through accurate dimensional calculations and punching force administration. Besides, it’s also best to use the best metal blanks that seamlessly flow and is less affected by heat. Some defects in metal deep and shallow drawing processes include the following.
Thinning and Tearing
Thinning overstretches a metal blank, especially if the punch force goes overboard. Miscalculations are typical causes, but it sometimes happens if the blank metal material doesn’t have the physical capability to handle the tension, even for correctly calculated punch force and speed. Similarly, tearing is likely when the sheer is excessive, rendering the formed metal part useless. Tearing at the edges of the finished part can be corrected by trimming, but thinning is irreversible.
Surface Defects
The shear can be excessive due to friction leading to metal scratching, denting and breaking. The issue is a compromise of the aesthetic finishing rather than an actual serious defect, and metal drawing operators can quickly correct it. Surface treatments like layering, polishing, and color-coating can eliminate the defect. However, it becomes quite a task if the surface defects can’t be reversed, rending metal parts less helpful.
Wrinkling
Wrinkling usually occurs in the vertical wall flange, and the problem is typically expected in metal deep drawing operations. The sheer force can be marginally excessive, causing wrinkling and making the finished metal part less quality. Wrinkling is irreversible and causes permanent distortion, which is a defect that most metal stamping manufacturers dread. However, correcting it is easy if it happens due to high holding pressure on blank holders, and trimming should remove such deformed areas.
Deep Drawing and Shallow Drawing Applications
Deep and shallow drawing products are practically helpful in a vast array of fields, including automotive, aerospace and electronics. Some typical applications of deep-drawn products include making kitchen utensils, fire extinguishers and water faucets. However, a high chance exists for virtually every field using hollow metal that they’d outsourced drawn products.
Almost every electric appliance and automotive machinery uses deep or shallow drawn metal Parts. A perfect example is the car engine system with piston cylinders and valves. Also, most builders’ hardware obtains their metal parts from drawn metal parts, and the aerospace industry gets a fair share too. The applications for both deep and shallow drawn metal parts are infinite, and a lot more other fields and industries utilize them.
Advantages of Deep Drawing and Shallow Drawing
Deep and shallow drawing processes have the edge over other metal forming procedures. A more apparent upside is that the process is usually straightforward and doesn’t require more complex die designs or sophisticated bending and cutting. Here’s why metal drawing is much preferred compared to other processes forming similar parts.
No Skilled Operators Needed
Unlike metal stamping and other forming processes, deep and shallow drawing need no operators. The processes are straightforward; perhaps, a human hand can help dislodge the formed parts and lubricate the dies. Some stamping operations are wholly automated, and no human intervention is necessary.
Little Set-Up Costs
Deep and shallow drawing processes don’t require hefty capital and investment compared to other metal forming processes. Usually, designing complex dies, such as progressive dies, can be back-breaking since you need professional software and CAM machining. However, deep and shallow drawing dies are minimalist, with no complex dents and ridges needed. That makes it less costly and affordable, although the produced parts may not substitute most other parts from different metal forming processes.
Operations are Usually Quick.
Deep and shallow drawing operations are usually quick and efficient. That’s because the entire process involves deforming a black as plainly as possible with no cutting or engraving. It’s even better when the calculations are correct and the force is metered and measured. It’s easy to produce high volume runs in metal drawing processes than in other forming processes, making it a preferred method.
Produces Strong Parts
Drawn metal parts from the two processes are usually sturdy since it works beyond the metals’ crystal structures. That locks the movement, making the metal part stronger. Unlike other forming processes, metal parts from the shallow and deep drawing process are more reliable and robust and can withstand sheer force in machinery architecture.
Incredible Accuracy
The chances of defects are minimal in metal drawing processes, and more credit is on the tooling used. Unlike other metal forming processes, progressive die stamping, for instance, tooling, can be complex and incredibly demanding, allowing room for fault and dimensional error. However, the simplicity in metal drawing tooling makes it seamless, creating highly precise tooling dimensions, making metal drawn parts more accurate and incredibly reliable.
Conclusion
Metal drawing is among the earliest metal forming processes in industrial manufacturing since virtually every machinery and electronic components utilize its parts. The more subordinate processes, shallow and deep metal drawing, are more practical and help various industries manufacture machinery and electronic parts. These two metal drawing processes aren’t so varied, although they have a little nuance and a thin line telling them apart. Mainly, the DDR tells them apart. Regardless, spotting a deep-drawn metal isn’t rocket science, and telling it apart from the shallow-drawn part is quite a breeze. It’s apparent that these two processes will remain significant even as the manufacturing world evolves into a more sophisticated facet.
2 Responses
Their comic timing is great, and can still deliver the emotions when you need them to.
buenas noches, grand blog on lardy loss. aforesaid helped.