Dive into the intricate world of progressive die stamping, a marvel of modern manufacturing. How does this technique cater to the creation of complex parts, and what sets it apart in the realm of metal stamping?
Progressive die stamping is a cutting-edge method that sequentially processes metal sheets through multiple stations, each performing a specific action, to produce intricate parts. It’s renowned for its efficiency, precision, and ability to handle complex designs with ease.
But what’s the magic behind this method? How does it seamlessly bring to life intricate designs, and why is it the go-to choice for complex parts? Join us as we unravel the mechanics, benefits, and nuances of progressive die stamping.
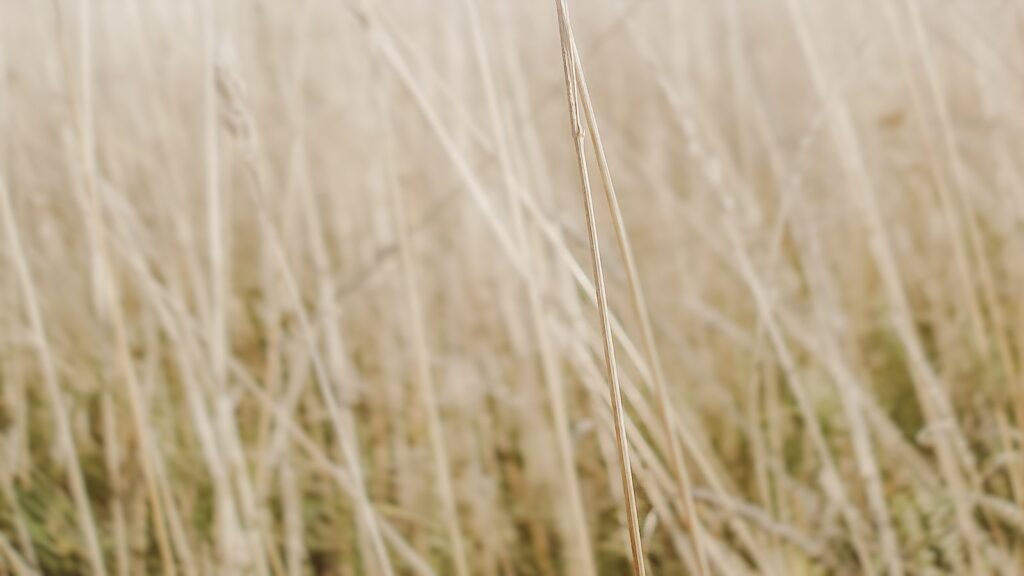
Progressive Die Stamping
In the vast realm of metalworking and manufacturing, progressive die stamping stands as a beacon of modern innovation. This technique, though intricate in its operations, offers unparalleled efficiency and precision, especially when it comes to producing complex parts. As industries evolve and demand more sophisticated components, the significance of progressive die stamping in today’s manufacturing landscape cannot be overstated.
The Process Unveiled
Progressive die stamping, as the name suggests, is a progressive process. It involves a metal strip being fed through a series of stations, each performing a specific operation, until the final part is produced. Here’s a step-by-step breakdown:
- Feeding: A metal strip is fed into the stamping press.
- Piloting: The strip is correctly positioned using pilot pins.
- Stamping: As the strip advances, it moves through a series of stations. Each station performs a specific action such as punching, bending, coining, or cutting.
- Progression: After each action, the strip progresses to the next station, getting closer to the final shape with each step.
- Ejection: Once the part has passed through all the stations and is fully formed, it’s separated from the strip and ejected.
The heart of this process is the die – a specialized tool designed to perform the stamping. The die’s “progressive” nature refers to its multiple stations, each dedicated to a specific task, ensuring that the metal undergoes a series of transformations in a single pass.
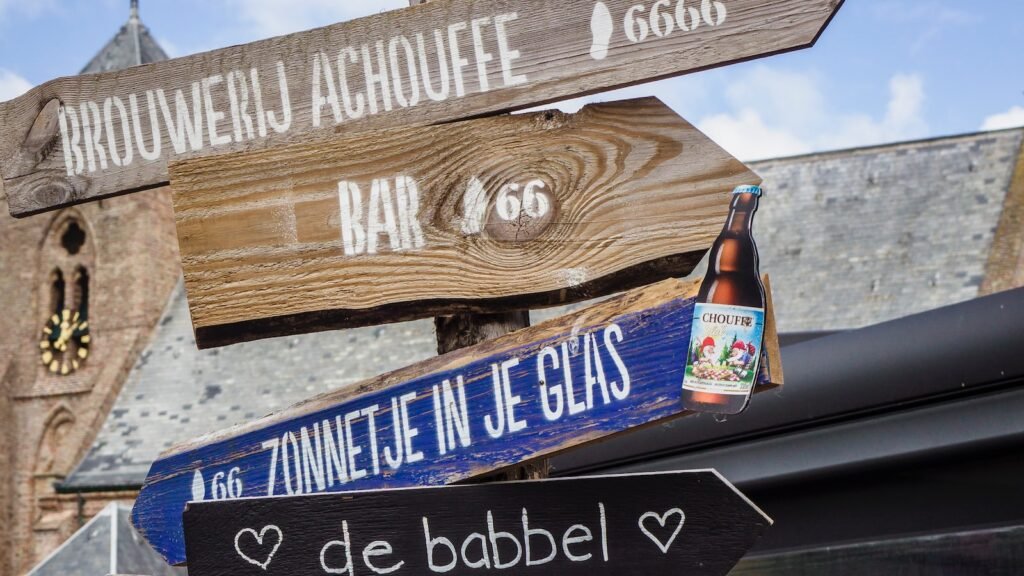
Why Complex Parts?
The beauty of progressive die stamping lies in its ability to produce intricate and detailed parts with impeccable precision. But what makes it especially suited for complex designs?
- Precision in Repetition: The method is designed for high-volume production. Once set up, it can produce thousands, if not millions, of identical parts, each matching the exact specifications of the design.
- Efficiency: The continuous feed of material and the multi-station design mean that multiple parts are being worked on simultaneously. This results in a rapid production rate, making it ideal for large orders.
- Material Conservation: The process is designed to minimize waste. The progressive nature ensures that as much of the metal strip is used in the final product as possible.
When compared to other stamping methods, progressive die stamping stands out for its ability to handle intricate designs in a cost-effective manner. While methods like transfer die stamping or tandem press stamping have their merits, they often require more manual intervention or are better suited for larger parts. For detailed, complex components, especially in high volumes, progressive die stamping is the go-to choice for many manufacturers.
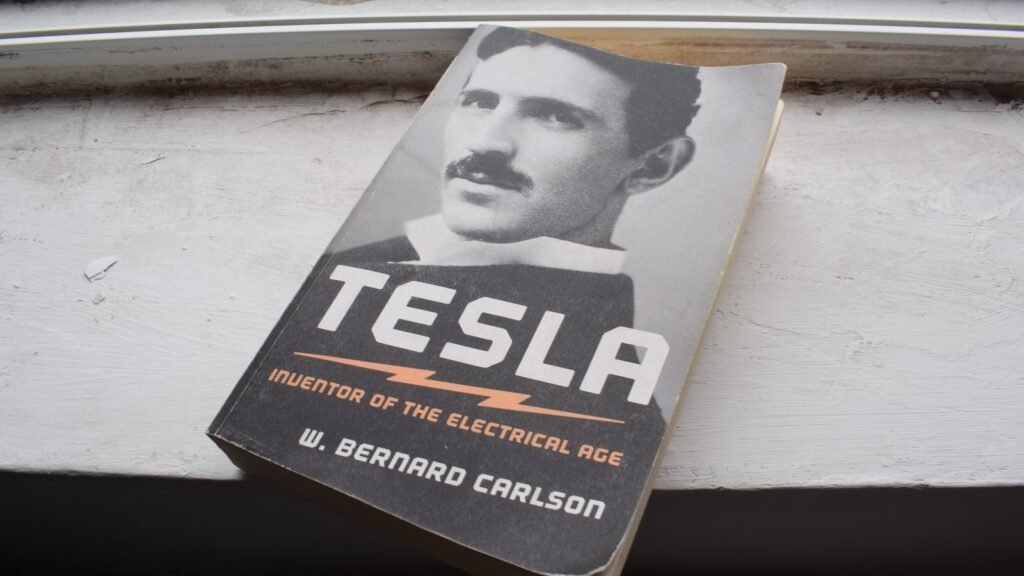
Advantages of Progressive Die Stamping for Complex Parts
Progressive die stamping, with its intricate yet efficient process, offers a plethora of advantages, especially when it comes to crafting complex parts. These benefits not only ensure top-notch product quality but also contribute to sustainable and cost-effective manufacturing. Let’s delve into the key advantages:
Precision and Consistency
One of the standout features of progressive die stamping is its unparalleled precision. Here’s how it ensures every part is a mirror reflection of the other:
- Tailored Dies: Each die is meticulously designed to match the exact specifications of the part. This ensures that every punch, bend, or cut is precise down to the minutest detail.
- Automated Process: The automated nature of the process eliminates the inconsistencies that might arise from manual operations. This means that whether it’s the first part or the ten-thousandth, each will be identical to the last.
- Quality Control: Modern stamping presses often come equipped with sensors and monitoring systems that continuously check the parts for any deviations, ensuring that any anomalies are detected and rectified immediately.
Speed and Efficiency
In the fast-paced world of manufacturing, time is of the essence. Progressive die stamping shines in this aspect:
- Simultaneous Operations: As the metal strip progresses through the die, multiple operations are performed simultaneously at different stations. This parallel processing significantly reduces the time taken to produce each part.
- Continuous Feed: The continuous feeding of the metal strip ensures that there’s no downtime between the production of parts, leading to a seamless and rapid production cycle.
- Cost-Effective: The speed and efficiency of the process translate to reduced production costs, especially when producing parts in large volumes. The initial setup might be resource-intensive, but the long-term benefits in terms of reduced per-part costs are substantial.
Reduced Waste
In an era where sustainability is paramount, the waste-reducing capabilities of progressive die stamping are a boon:
- Optimized Material Use: The design of the dies and the process ensures that the maximum amount of the metal strip is used in the final product, minimizing offcuts and wastage.
- Recycling: Any waste that is produced, like trimmings or punched out sections, can be easily collected and recycled, ensuring that there’s minimal material wastage.
- Environmental Benefits: Reduced waste means fewer resources are needed to produce the same number of parts. This, coupled with the recycling aspect, ensures that the environmental footprint of the manufacturing process is minimized.

Challenges and Considerations in Progressive Die Stamping
While progressive die stamping offers a myriad of advantages, it’s not without its challenges. Like any manufacturing process, it requires careful consideration and understanding of its limitations to harness its full potential. Let’s delve into some of the challenges and considerations associated with this method:
Design Limitations
Every manufacturing technique has its constraints, and progressive die stamping is no exception:
- Complexity Constraints: While the method is ideal for complex parts, there’s a limit to the intricacy it can handle. Extremely intricate designs might require multiple dies or alternative methods.
- Material Thickness: Progressive die stamping works best with specific material thicknesses. Too thick or too thin materials can pose challenges in terms of die design and stamping efficiency.
- Die Design: The design of the die itself can be challenging. It needs to account for the material’s properties, the desired final shape, and the sequence of operations.
Tips for Optimal Design:
- Collaboration: Engage with experienced die designers during the product design phase to ensure the design is feasible for progressive stamping.
- Prototyping: Before finalizing the die, create prototypes to test the design and make necessary adjustments.
- Material Consideration: Choose materials that are well-suited for the stamping process, considering factors like malleability and tensile strength.
Maintenance and Wear
The continuous and high-speed nature of progressive die stamping means the dies are subjected to significant wear and tear:
- Regular Wear: Each stamping action, though minute, contributes to the wear of the die. Over time, this can lead to reduced precision and quality of the stamped parts.
- Lubrication: Friction between the die and the metal strip can accelerate wear. Regular lubrication is essential to reduce this friction and prolong the die’s life.
- Material Issues: Using materials that are harder than the die or contaminants in the material can lead to premature wear or even damage.
Maintenance Tips:
- Regular Inspection: Periodically inspect the dies for signs of wear or damage. Early detection can prevent more significant issues down the line.
- Scheduled Maintenance: Have a routine maintenance schedule. This includes cleaning, lubrication, and minor repairs.
- Replacement Parts: Keep essential replacement parts on hand. This ensures minimal downtime in case of wear or damage.
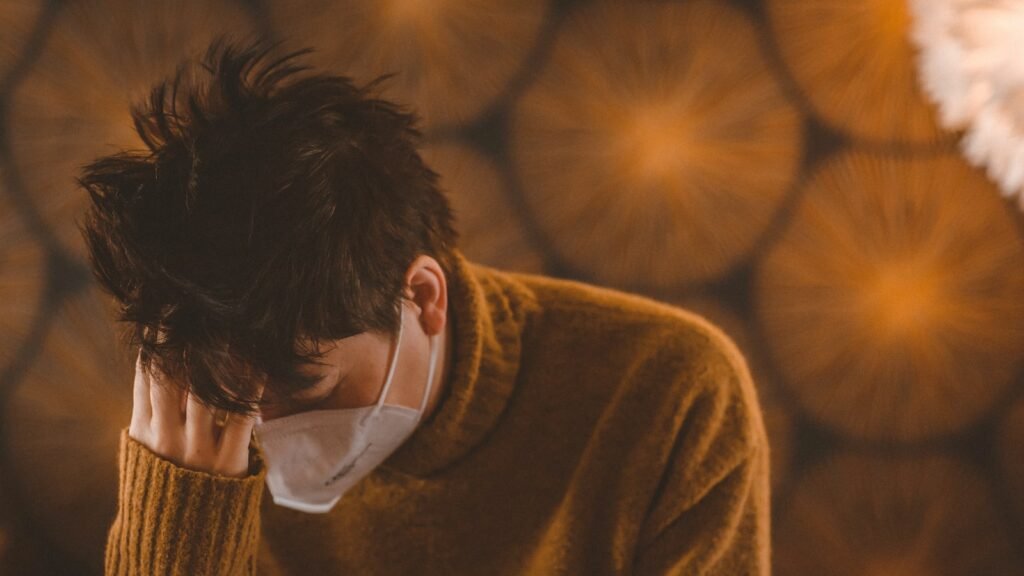
The Future of Progressive Die Stamping
The manufacturing world is in a state of constant evolution, driven by technological advancements and innovative practices. Progressive die stamping, a stalwart in the realm of metalworking, is no exception. As we look to the horizon, several emerging trends and technologies promise to redefine the landscape of this age-old technique.
Technological Advancements
- Artificial Intelligence (AI): AI is poised to play a transformative role in progressive die stamping. With its ability to analyze vast amounts of data, AI can optimize the stamping process by predicting wear and tear, adjusting parameters in real-time for optimal results, and even assisting in the design of dies for maximum efficiency and precision.
- Advanced Sensors and Monitoring: The integration of advanced sensors can provide real-time feedback during the stamping process. This can lead to immediate adjustments, ensuring consistent quality and reducing wastage. For instance, sensors can detect material inconsistencies or temperature fluctuations that might affect the stamping quality.
- Robotics and Automation: While progressive die stamping is already an automated process, the integration of advanced robotics can further enhance precision, especially for complex parts. Robots can handle materials with greater accuracy, ensure optimal positioning, and even assist in maintenance tasks.
- 3D Printing: While traditionally used for prototyping, advancements in 3D printing materials and techniques might allow it to be used in conjunction with stamping. For instance, creating specific parts of a die or even producing short runs of stamped parts.
Predictions for the Next Decade:
- Integration of Virtual Reality (VR) and Augmented Reality (AR): These technologies can revolutionize the design phase, allowing engineers to visualize and test die designs in a virtual environment before production.
- Sustainability Focus: As industries worldwide shift towards sustainable practices, we can expect innovations in progressive die stamping that reduce energy consumption, minimize waste, and utilize eco-friendly materials.
- Customization: With advancements in technology, producing customized stamped parts in smaller batches might become more cost-effective, catering to niche markets and specific customer demands.
- Collaborative Manufacturing: The future might see a more collaborative approach to manufacturing, with progressive die stamping being integrated seamlessly with other techniques and processes for a holistic production approach.

Conclusion
In essence, while we’ve explored the profound impact of progressive die stamping on manufacturing complex parts, it’s evident that its journey is far from over. As we stand at the cusp of a new era in manufacturing, progressive die stamping not only holds its ground but also beckons a future replete with innovations, advancements, and endless possibilities. It’s a testament to the enduring relevance of this age-old technique and its boundless potential for the future.