The diverse manufacturing methodologies of steel provide a spectrum of materials with distinct properties. Among these, hot rolled and cold rolled steel emerge as predominant forms, each with its unique characteristics and applications. This article delineates the key differences between hot rolled and cold rolled steel, helping you to make informed decisions based on your project requirements.
Hot rolled steel is processed at temperatures above the recrystallization temperature of steel, making it easier to shape and form, while cold rolled steel is processed below the recrystallization temperature, offering a higher surface finish and more precise dimensions.
Delve deeper as we dissect the contrasting production processes, the resultant material properties, and the suitable applications for both hot rolled and cold rolled steel, guiding you through a comparative lens to discern their distinctness.
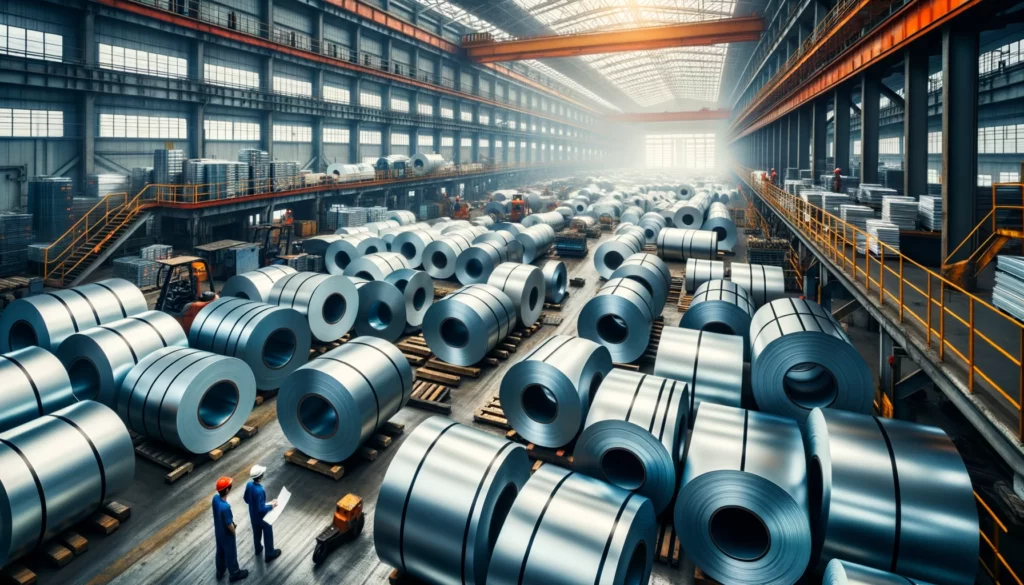
Understanding the Production Processes
The journey of transforming raw steel into usable forms entails a medley of manufacturing processes, each with its unique set of parameters and outcomes. Hot rolled and cold rolled steel, the two predominant forms, are birthed through distinct production processes that significantly influence their characteristics and applications. Here, we delve into the manufacturing journey of both, elucidating the temperature regimes and mechanical processing involved in their creation.
Hot Rolled Steel: The High-Temperature Craft
The saga of hot rolled steel commences in the realm of high temperatures, specifically above the steel’s recrystallization temperature, typically around 1700°F (927°C). This high-temperature milieu makes the steel malleable, enabling it to be easily manipulated and formed into various shapes. The process unfolds as follows:
- Heating: Initially, the steel is heated to a temperature high enough to allow recrystallization, making it pliable and ready for rolling.
- Rolling: Post heating, the malleable steel is passed through large rollers that shape it into the desired form, whether it be sheets, bars, or rods.
- Cooling: Once shaped, the steel is left to cool naturally to room temperature, solidifying its form.
Cold Rolled Steel: The Pursuit of Precision
Contrastingly, the narrative of cold rolled steel is one of precision and fine finish, achieved in the cooler domain, below the steel’s recrystallization temperature. The journey encompasses:
- Rolling: Unlike hot rolled steel, the cold rolling process commences with steel that has already been cooled to room temperature. This steel is then passed through rollers, under high pressure, to achieve the desired dimensions and surface finish.
- Annealing: To alleviate the stresses induced during rolling and to attain desired mechanical properties, the steel is subjected to a process called annealing, where it’s heated below its recrystallization point and then slowly cooled.
- Tempering: This step involves moderately reheating the steel to enhance its toughness and reduce brittleness, fine-tuning its mechanical properties to meet the desired specifications.
The dichotomy between hot and cold rolled steel’s production processes delineates a clear distinction in their characteristics and applications. While hot rolling bequeaths a rougher surface but a form easier to shape, cold rolling delivers a smoother finish and more precise dimensions, making each suitable for specific applications in the industrial cosmos. The knowledge of these processes is pivotal as it guides the choice between hot rolled and cold rolled steel, aligning with the requirements and constraints of the project at hand.
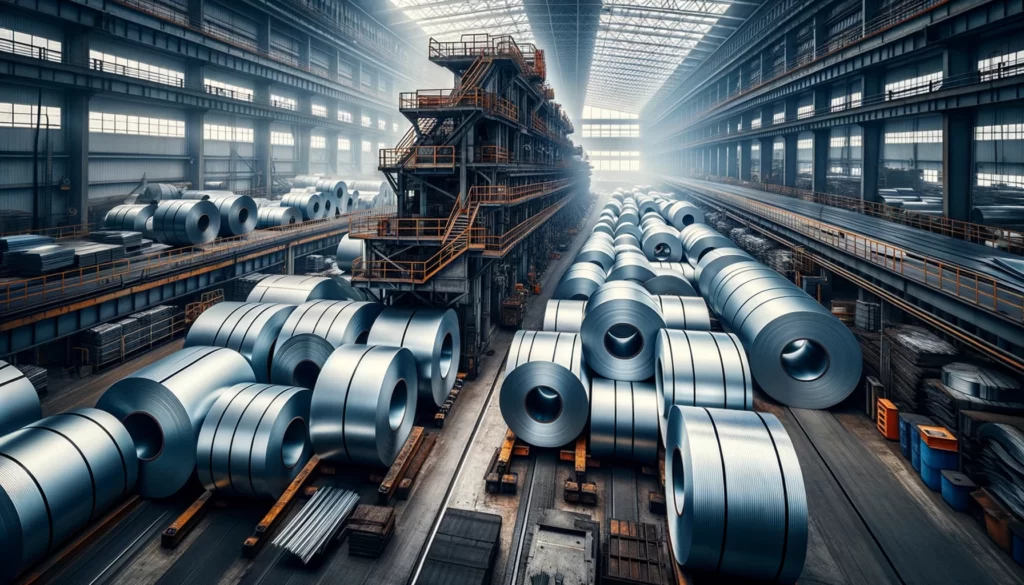
Material Properties: A Contrast
The divergent production processes of hot rolled and cold rolled steel not only carve their journey from raw steel to finished products but significantly shape their material properties. These properties, in turn, govern the performance and applications of the steel, making it imperative to delve into the contrasting characteristics bestowed by the hot and cold rolling processes.
Surface Finish and Dimensions
Hot rolled steel, due to its production at high temperatures, often exhibits a rougher surface finish. The process allows for great formability but less control over the final dimensions. On the contrary, cold rolled steel boasts a smooth, polished surface finish and tighter tolerances owing to its rolling process at room temperature. The precise dimensions rendered by cold rolling are often crucial in applications demanding high accuracy and aesthetics.
Strength and Hardness
The realm of cold rolling, with its additional processing like annealing and tempering, imparts higher strength and hardness to the steel when compared to hot rolled steel. The cold rolling process realigns the steel’s grain structure, leading to improved strength and hardness, albeit at the cost of reduced ductility.
Ductility and Formability
Hot rolled steel, due to its formative process at elevated temperatures, retains a higher degree of ductility and formability. This malleability makes it a preferred choice for structural projects where shaping, welding, or forging is integral. Cold rolled steel, although stronger, is less ductile, making it less suitable for such formative operations.
Internal Stress
Cold rolled steel often harbors internal stresses induced during the rolling process. These stresses can pose challenges in certain applications, especially those requiring precise shape or dimensional stability. Hot rolled steel, with its natural cooling, tends to have fewer internal stresses, making it more stable in some applications.
Cost
The comprehensive processing involved in cold rolling—particularly the additional steps of annealing and tempering—often translates to a higher cost compared to hot rolled steel. The cost factor, coupled with the material properties, plays a pivotal role in determining the choice between hot and cold rolled steel based on the project’s budget and requirements.
Applications: A Reflection of Properties
The contrasting properties of hot and cold rolled steel dictate their suitability for different applications. Hot rolled steel, with its superior formability, finds its essence in structural applications, construction, and welding projects. Conversely, cold rolled steel, with its high strength and precise dimensions, is the go-to material for applications demanding a smooth surface finish and exact measurements like automotive parts, appliances, and furniture.
In conclusion, the distinction in material properties stemming from the disparate rolling processes underscores the importance of making an informed choice based on the project’s demands. Whether it’s the formability of hot rolled steel or the precision and strength of cold rolled steel, understanding the material properties is quintessential in aligning with the project’s goals and ensuring optimal performance in real-world applications.

Applications and Industry Preferences
The tapestry of industrial applications paints a vivid picture of the diverse roles hot rolled and cold rolled steel play in the modern engineering and manufacturing landscapes. The distinct properties of these steel variants, shaped by their respective production processes, resonate with the unique demands of different industries. Here, we delve into the sectors that favor one over the other and dissect the rationale behind their preferences.
Hot Rolled Steel: The Backbone of Structural Projects
Hot rolled steel, with its inherent ductility and ease of forming, finds its core applications in industries where structural integrity is paramount.
- Construction: The construction industry heavily relies on hot rolled steel for structural elements like beams, channels, and angles which form the skeleton of buildings and bridges.
- Automotive: In the automotive sector, hot rolled steel is used for parts that undergo a significant amount of forming and bending like chassis and frames.
- Railroad Tracks: The production of railroad tracks often employs hot rolled steel due to its ability to withstand high stress and deform without breaking.
- Agricultural Equipment: The robust nature of hot rolled steel makes it a preferred choice for manufacturing durable agricultural equipment and machinery.
Cold Rolled Steel: The Emblem of Precision and Finish
Cold rolled steel, synonymous with precision, smooth finish, and strength, is the material of choice in industries where these attributes are non-negotiable.
- Automotive: Unlike its hot rolled counterpart, cold rolled steel is used for parts requiring a smooth finish and precise dimensions like body panels and interior components.
- Appliances: The sleek finish and dimensional accuracy of cold rolled steel make it a favored material for modern appliances like refrigerators, washing machines, and dryers.
- Furniture: The aesthetic appeal and strength of cold rolled steel resonate well with furniture manufacturing, providing a blend of form and function.
- Electronics Enclosures: The precision and smooth surface finish of cold rolled steel are essential for electronics enclosures that demand tight tolerances and a professional appearance.
Bridging the Divide: Industry-Driven Choices
The industry-driven choices between hot rolled and cold rolled steel echo the intrinsic link between material properties and application requirements. While hot rolled steel is the go-to material for structural, high-stress applications, cold rolled steel, with its precise dimensions and polished appearance, caters to applications demanding a high level of finish and accuracy.
In a nutshell, the preference for hot or cold rolled steel is a reflection of the industry’s demand for certain material characteristics to meet specific application requirements. The understanding of these preferences not only facilitates an informed material selection but also underscores the versatility and essential role of steel in propelling modern industrial and manufacturing endeavors.
Conclusion
Navigating through the nuances of hot and cold rolled steel reveals a clear demarcation in their production processes, material properties, and industry preferences. Hot rolled steel, with its formability and structural integrity, caters to industries like construction and automotive where shaping and welding are pivotal. Conversely, cold rolled steel, synonymous with precision and smooth finish, finds its essence in applications demanding accuracy and aesthetics, such as appliances and furniture manufacturing.
The informed choice between hot and cold rolled steel, aligned with the project’s demands, not only optimizes performance but also ensures cost-effectiveness. Understanding these differences is fundamental in making insightful material selections, thus steering the projects towards success and sustainability in the long run.