In the complex world of manufacturing, where precision and innovation go hand in hand, material selection is not just a technical issue, but a critical decision that determines the nature of the product. This article will reveal the nuances of choosing the right stamping die material. Just as a conductor carefully selects each instrument to compose a symphony, a manufacturer must carefully select materials to make a project a success.
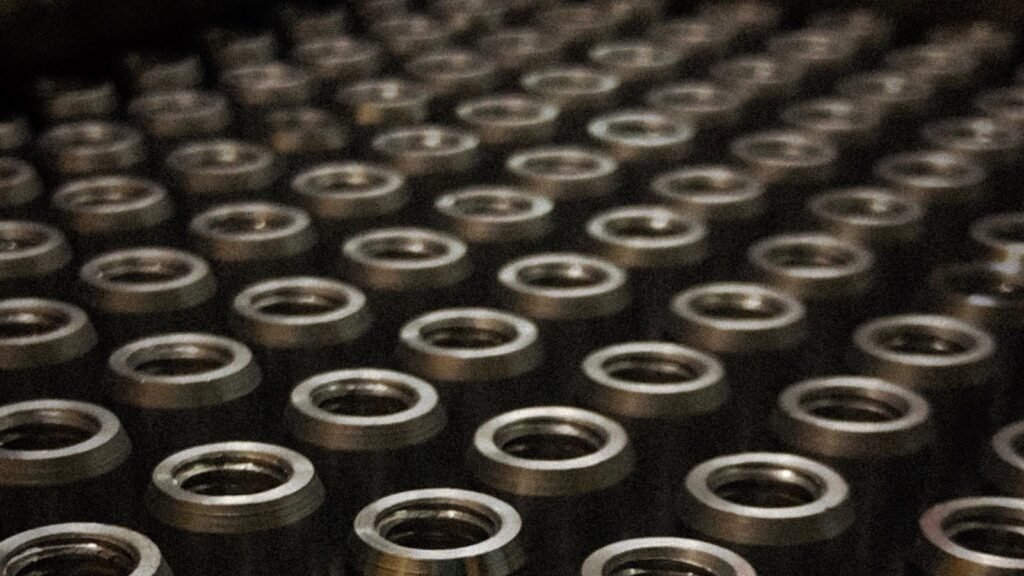
Understanding Mold Requirements
Before diving into material choices, a profound understanding of mold requirements is essential. For instance, consider a project to create intricate automotive components – the material selected must exhibit not only durability but also the ability to withstand high pressures and temperature variations. In a real-world example, a manufacturer producing critical suspension parts would opt for high-strength steel molds to ensure longevity under intense operational conditions.

The Power of Tool Steels
Tool steels are the workhorses of stamping mold materials. For example, D2 tool steel boasts excellent wear resistance and toughness, making it suitable for high-precision molds used in industries like aerospace. In practice, a company manufacturing precision gears would opt for D2 tool steel molds to maintain tight tolerances and ensure smooth gear engagement in their end products.

The Power of Powdered Steel
Powdered steel has transformed stamping dies with its superior durability and precision. Its unique combination of hardness and toughness makes it ideal for industries that require high-pressure stamping while maintaining complex designs. From aerospace to consumer electronics, ASP23、ASP60 ensures impeccable results and has revolutionized the world of stamping dies.

The Elegance of Aluminum
Aluminum alloys are a unique combination of lightweight construction and strength. In stamping die applications, aluminum alloys are often chosen for die holders because of their superior ability to withstand the stamping process while controlling weight.

An insight into the world of tungsten carbide
Carbide materials, such as tungsten carbide, offer unparalleled hardness and wear resistance. These materials shine in projects involving abrasive materials. In the real world, manufacturers of mining equipment components use tungsten carbide tooling to resist the abrasive nature of mining materials, thereby extending the life of the tooling. Examples: KD20, CD650, CF-H40S, and more!

Polymers: The Unconventional Choice
Polymer materials are emerging as unconventional yet effective choices. In projects where intricate designs or unique textures are essential, polymers like PEEK (Polyether Ether Ketone) thrive. For example, a company specializing in consumer electronics might opt for PEEK molds to achieve intricate designs in smartphone casings.

The Dance of Temperature: High-Temperature Alloys
Industries like automotive and aerospace often require molds that can withstand high temperatures. High-temperature alloys, like Inconel, excel in such scenarios. A practical example would be a manufacturer producing exhaust components – using Inconel molds ensures that molds remain structurally stable under extreme heat conditions.

The Eco-Friendly Conundrum
In an era of environmental consciousness, choosing eco-friendly materials becomes imperative. Biodegradable materials and recycled alloys are gaining traction. In a tangible case, a company producing packaging materials might prioritize biodegradable molds to align with their commitment to sustainability.

Conclusion
Selecting the right material for stamping molds isn’t just a technicality – it’s a strategic decision that defines the trajectory of a project. Just as a composer weaves melodies to create harmony, manufacturers intricately choose materials to craft precision, durability, and innovation. By understanding project requirements, exploring a spectrum of materials, and aligning with industry demands, manufacturers create not just molds but instruments of success that shape the future of manufacturing.