Before deciding to work with computer numerical control (CNC) machining or metal stamping, several factors come into play. The critical consideration is cost as it relates to metal stamping vs. CNC machining. Another key factor is production speed. CNC machining has a slower production rate than does metal stamping.
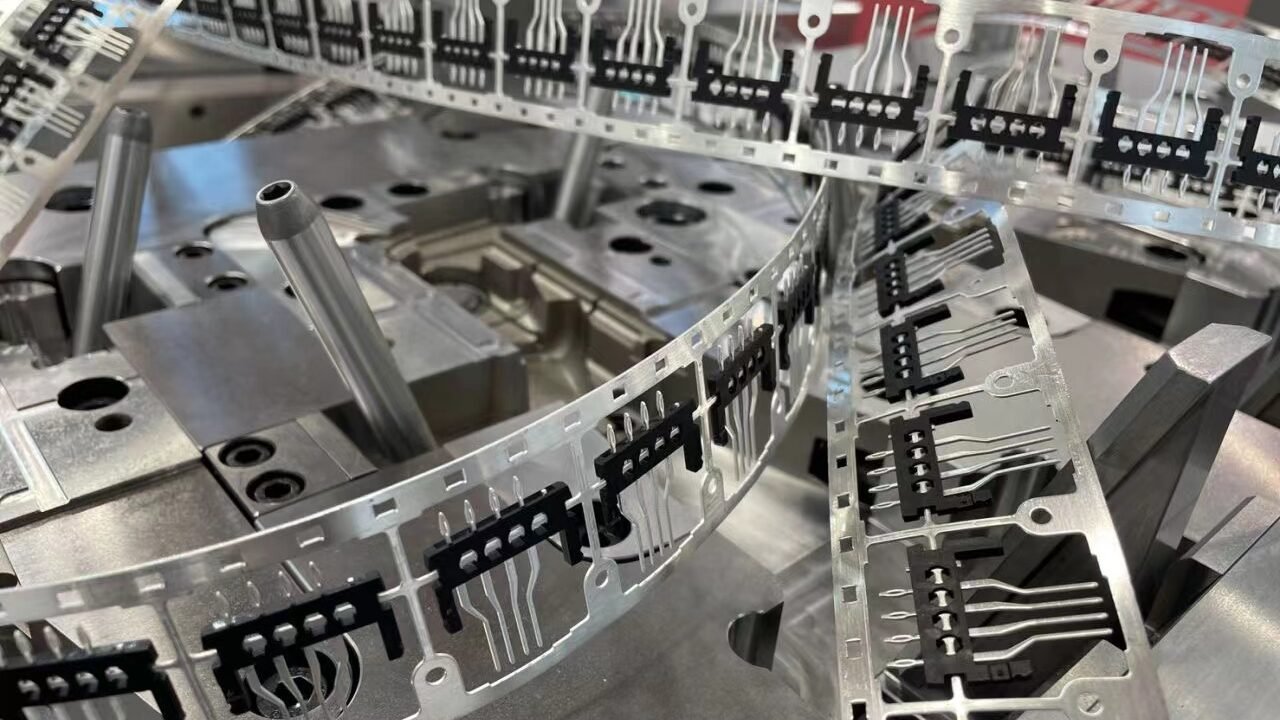
Three factors to consider prior to choosing metal stamping or CNC machining are…
- Material tolerance
CNC works best with materials that offer low tolerance than metal, which can be easily shaved or bent to desired shapes. - Quantity
Metal stamping is ideal for mass production, while CNC works with relatively low quantity production. - Price
Price is a crucial factor in any production process, considering tolerance elements. Although CNC is slow, it’s accurate but pricey, while stamping is relatively cheap.
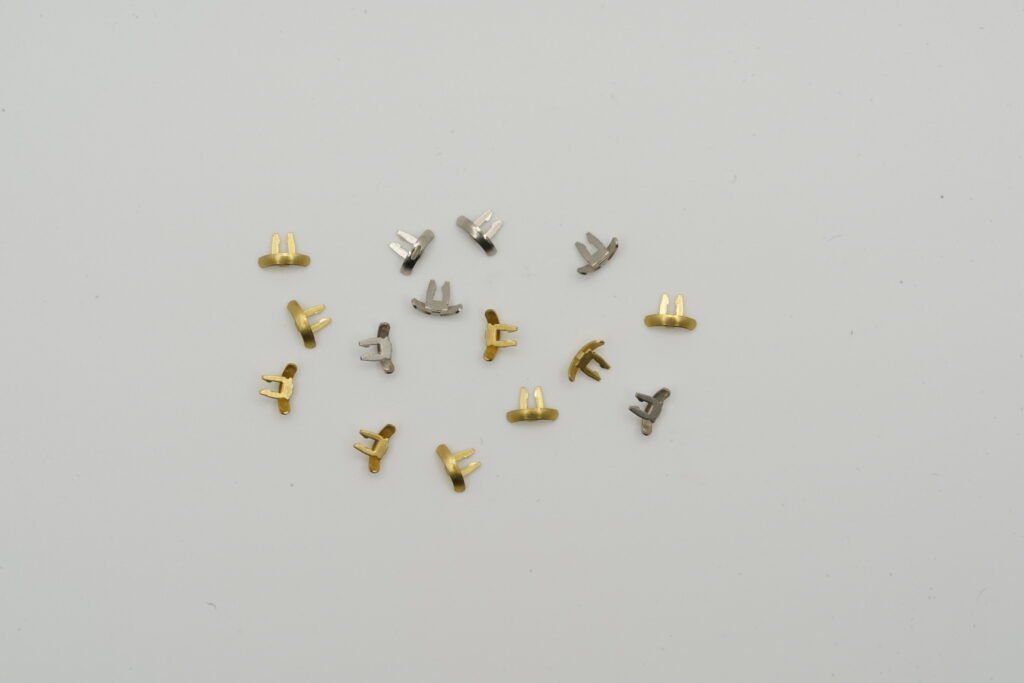
Metal stamping
Metal stamping is a term that refers to various techniques of converting metal sheets into various shapes. It involves drawing and blanking processes that stretch and cut metal sheets in two or three dimensions.
Stamping is executed by tools attached to a pressing machine. Ordinarily, a die and punch work together to bend, stretch, and blank a metal sheet to the ideal shape. The process can also use piercing and other operations.
From the writer
Metal stamping is a relatively cheap and fast way of production compared to CNC machining. It’s preferred when speed is a crucial consideration, but it’s not preferred when complex shapes are needed. However, a CNC machine takes a shorter setup time, and once a program is designed in a CAD file, the production begins.
Specialties of Metal Stamping
Modernization has fueled the demand for metal sheets to aid the manufacturing of various machines. As a result, more reliable means of production have been devised to efficiently create replicas of metal designs. This has led to innovations in metal stamping, making it popular among manufacturers.
Automation and other innovations have allowed stamping for complex designs and lower production times. Besides, metal stamping can produce several metal designs simultaneously, making it a preferred means of production among car manufacturers.
Here are highlights of the various processes used in metal stamping:
• Notching
• Bending
• Embossing
• Stamping
• Tooling
• Punching
Also, metal stamping uses the following alloys for precision production in a variety of industries.
- Brass alloys
- Aluminum alloys
- Copper alloys
- Steel and stainless steel
- Nickel alloys
Production Capability
Metal stamping has a higher production ability, and it’s faster and more versatile. Although getting the pressing machine ready for production takes time, it’s smooth sailing once set up properly. In short, the production capacity is higher compared to CNC machining.
Production speeds
While complex designs are difficult to stamp, metal stamping is the fastest way to produce metal shapes. Its production speed is unmatched when the production line is functional. Metal stamping cannot create complex engine blocks or cylinder heads. Stamped parts may need to go through another level of processing before use to achieve higher accuracy post-production.
Tools used in metal stamping
The type of tools used in metal stamping depends on the product. For instance, you will need different tools from producing car parts than for producing metal medical equipment. Also, hard tooling offers a low cost of production compared to soft tooling.
Here is a collection of the different tools used in metal stamping.
• Progressive Dies
• Deep Drawing Diesling
• Compound Dies
• Single Dies
Accuracy
The molds used in pressing metal sheets ensure precise shapes. However, the type of material used plays a crucial role in determining the accuracy of the output.
Adaptability
For metals to be pressed, they need flexibility. Stamping is an efficient and flexible means of producing complex metal designs. However, some materials need further treatment, such as heat treatment. Also, it’s not suitable for rigid materials because of cracking. Also, sheet thickness affects the production technique, since thicker sheets are more prone to deformation.
From the writer
Metal stamping is an efficient means of production that can be used across various industries. Medical equipment producers, for example, prefer working on contract, as medical apparatus are diverse and keep changing. Other manufacturers such as carmakers and producers of airplane parts settle on metal pressing as it’s efficient and accurate.
Product shapes
Metal stamping is a reliable and efficient way of producing parts from metal sheets in bulk. Production is efficient and accurate once the initial mold is designed and mounted onto the presser. Remember, metal stamping can create complex designs thanks to innovative technology and provide excellent results.
CNC Machining
The CNC process involves carving a shape from a solid bar or tubing. CNC is a prismatic method, as the workpiece is held in a fixed position while a tool excavates a design from it. Milling is a classic example of the chromatic process that aids in cutting materials into the desired shape.
CNC stands for Computer Numerical Control, which refers to how a machine tool is controlled to produce the desired shape. A CNC machine comprises an axis motion powered by the spindle. One device may contain several spindles that receive their commands from a computer program that guides each one of them to give the needed geometry.
Specialties of CNC Machining
CNC machines combine the use of several tools to perform their essential functions. The machines run on one or two axes, while advanced ones operate on the x, y, and z-axis. They can flip parts to allow the removal of materials that were underneath. This eliminates the need for workers to convert the prototype.
Production Capability
CNC refers to two categories—novel and conventional machining technology. Each type offers its unique capabilities, and you have to make your choice based on the operating characteristics.
Production Speeds
While the automotive industry efficiently works with metal stamping, medical and aircraft production requires the higher precision offered by CNC. CNC machining provides the highest precision while producing identical bulk parts. The systems come with quality control checks to ensure the speed of production and quality of output are not compromised.
CNC machining benefits several manufacturing industries, as its techniques are reliable and efficient. Using high technology and innovative tools makes the production process efficient, and one can achieve better results with tight tolerance materials.
Tools
CNC machines are a versatile apparatus that use a range of high-tech tools to deliver accurate results. The tools range from thread and end mills to ensure efficient and reliable products. Every tool performs a specific task, ranging from incisions to cuts. Here is a collection of CNC tools.
- Roughing end mill
- End mill
- Fly cutter
- Thread mill
- Reamer
- Drill bit
- Hollow mill
- Slab mill
- Gear cutter
- Side and face cutter
- Face mill
Accuracy
As is true of all cutting and machining strategies, different constituents have unique behaviors. The size and form of a part even have an enormous impact on the method. However, the CNC technique offers benefits over alternative strategies.
This is because of CNC can deliver:
• High accuracy regarding tolerances
• Exceptional surface finishes, as well as custom finishes
• Repeatability, even at high volumes
A talented artisan will use a manual shaper to form a high-quality product, but what happens when you need quantities of ten, one hundred, or 10,000 parts?
Adaptability
First, in CNC machining technology, there is initial analysis, fixture-evaluation, and strategies to judge the adaptive CNC method and fixture style. Second, a machining fixture is made once its positioning theme, clamping theme, materials, and structural characteristics are established.
Product shapes
Depending on the material’s complexity, and also the economic factors at play, choices are made, including 3D printing and fused deposition modeling (FDM) machines, as well as other options. FDM machines can produce advanced shapes and internal components more quickly than a CNC machine. 3D printing provides product designers and manufacturers flexibility that CNC machines cannot provide.
In contrast, typical CNC machines are restricted by the tools available and the axis of rotation the machine will use. CNC machines can still be used with a range of materials, however, these machines operate on a comparatively strict set of restrictions related to the various materials used.
So, what is the correct choice?
Your choice is dictated by quantity and design. High production volumes suggest metal stamping, as it minimizes production costs because higher material utilization of stamping keeps costs low. This can be vital when operating with expensive specialty materials or exotic alloys.
CNC machining is preferred for advanced components that require tight tolerances.