In the world of manufacturing, achieving precision in high-volume metal stamping is both a challenge and a necessity. As demand surges, ensuring each stamped component meets stringent quality standards becomes paramount. But how do manufacturers maintain this precision consistently?
To maintain precision in high-volume metal stamping, manufacturers employ advanced machinery, implement rigorous quality control measures, and continuously train their workforce. By integrating these practices, they ensure that each stamped component is consistent in quality, regardless of the production volume.
Dive deeper to understand the intricacies of achieving precision in high-volume metal stamping and the strategies employed by industry leaders.

The Role of Advanced Stamping Machines
In the realm of metal stamping, the machinery used plays a pivotal role in determining the precision and quality of the final product. Over the years, the evolution of these machines has been nothing short of revolutionary, ensuring that manufacturers can meet the ever-increasing demands for precision, especially in high-volume production scenarios.
Evolution of Stamping Machines: From Manual to CNC-Controlled Systems
The journey of stamping machines began with manual systems, where operators had to manually set and operate the machinery. These systems, while effective for their time, had limitations in terms of speed, consistency, and precision. As technology progressed, the industry saw the introduction of Computer Numerical Control (CNC) systems. These machines, controlled by computerized systems, brought about a paradigm shift in metal stamping. With CNC-controlled systems, manufacturers could achieve intricate designs, tighter tolerances, and faster production rates. The automation ensured that each stamped piece was virtually identical to the last, eliminating the inconsistencies that were prevalent with manual systems.
How Modern Machinery Ensures Consistent Force and Alignment
One of the standout features of modern stamping machines is their ability to apply consistent force throughout the stamping process. This is crucial because even a slight variation in force can lead to defects or inconsistencies in the final product. Advanced sensors and feedback loops in these machines monitor the force in real-time, making micro-adjustments as needed to maintain consistency.
Furthermore, alignment is another critical factor in stamping. Modern machines come equipped with precision alignment systems that ensure the metal sheet is perfectly positioned before each stamp. This not only ensures the accuracy of each stamp but also reduces the chances of wear and tear on the tools, thereby extending their lifespan.
The Significance of Regular Machine Maintenance and Calibration
While advanced machinery has undoubtedly enhanced the precision and efficiency of metal stamping, it’s essential to understand that these machines require regular maintenance and calibration to function optimally. Regular maintenance ensures that all components of the machine are in perfect working condition, reducing the chances of unexpected breakdowns.
Calibration, on the other hand, is vital to ensure that the machine operates within the specified tolerances. Over time, even the most advanced machines can drift out of calibration due to regular wear and tear. By periodically calibrating the machinery, manufacturers can ensure that each stamp is as precise as the last, maintaining the high standards that the industry demands.

Quality Control – The Backbone of Precision
In the world of high-volume metal stamping, achieving consistent precision is not just about the machinery or the materials used; it’s also about the systems in place to monitor and ensure that quality is maintained at every step of the process. Quality control, in this context, becomes the backbone of precision, ensuring that every stamped component meets the desired specifications and standards.
Implementing In-Line Inspection Systems for Real-Time Quality Checks
One of the most effective ways to ensure precision in high-volume metal stamping is to implement in-line inspection systems. These systems, often equipped with advanced sensors and cameras, continuously monitor the stamping process in real-time. They can detect even the slightest deviations from the desired specifications, allowing for immediate corrective actions. By catching potential issues early, manufacturers can reduce wastage, rework, and ensure that only quality components move to the next stage of production.
The Role of Statistical Process Control (SPC) in Monitoring Production Quality
Statistical Process Control (SPC) is a method used to analyze and control the quality of a production process. By collecting data from the production line and analyzing it using statistical methods, manufacturers can identify trends, variations, and potential issues. For instance, if a particular tool starts wearing out, it might cause a gradual shift in the dimensions of the stamped parts. SPC can detect such trends early on, allowing for preventive maintenance or tool replacement before the issue escalates. This proactive approach ensures that the production remains within the desired quality limits and that precision is maintained throughout.
Importance of Periodic Audits and Third-Party Certifications
While in-house quality control measures are essential, periodic audits and third-party certifications add an extra layer of assurance. External audits provide an unbiased view of the production process, identifying areas of improvement that might have been overlooked internally. Moreover, achieving third-party certifications, such as ISO standards, indicates that the manufacturer adheres to globally recognized quality standards. Such certifications not only enhance the brand’s reputation but also instill confidence in clients and stakeholders about the quality and precision of the stamped components.

Workforce Training and Skill Development
In the realm of high-volume metal stamping, while machinery and technology play pivotal roles, the human element remains irreplaceable. The workforce, with their skills and expertise, are the ones who operate these machines, make decisions on the shop floor, and ensure that the end product meets the desired standards. Hence, investing in their training and skill development becomes paramount.
The Need for Continuous Training in Handling Advanced Machinery
As technology evolves, so does the machinery used in metal stamping. New features, controls, and capabilities are regularly added to enhance precision and efficiency. However, these advancements are only as good as the operators behind them. Continuous training ensures that the workforce is updated with the latest machine functionalities. It enables them to leverage the full potential of the equipment, ensuring optimal performance and minimizing errors.
Role-Play and Simulation-Based Training for Real-World Scenarios
One of the most effective training methodologies is simulation-based training. By recreating real-world scenarios in a controlled environment, workers can practice their responses to various situations without the risk of causing actual production disruptions. Role-playing, on the other hand, helps in developing soft skills, such as communication and teamwork. For instance, a role-play scenario might involve a machine malfunction, where the operator, maintenance team, and floor manager must coordinate their actions. Such exercises not only enhance technical skills but also foster collaboration and problem-solving abilities.
Encouraging a Culture of Quality and Precision Among the Workforce
Beyond technical training, it’s essential to instill a culture of quality and precision among the workforce. When every individual, from the machine operator to the quality inspector, takes personal pride in the precision of their work, the overall quality of production naturally elevates. Regular workshops, feedback sessions, and recognition programs can be effective in promoting such a culture. Celebrating milestones, acknowledging individuals who consistently produce high-quality work, and creating a platform where employees can share best practices can go a long way in ensuring that the entire team is aligned with the organization’s quality objectives.

Material Selection and Its Impact on Precision
In the world of high-volume metal stamping, the choice of material is not merely about durability or cost-effectiveness. It’s about precision. The material used can significantly influence the accuracy of the final product, especially when dealing with large production volumes where even minor inconsistencies can lead to substantial discrepancies.
Importance of Using Consistent and High-Quality Raw Materials
Every metal or alloy has its unique properties, from malleability to tensile strength. Using high-quality raw materials ensures that these properties remain consistent throughout the production process. For instance, impurities in a metal can lead to unexpected behaviors during stamping, such as uneven bending or increased susceptibility to cracks. By sourcing consistent and high-quality materials, manufacturers can ensure that each stamped piece behaves predictably, maintaining the desired precision.
The Role of Material Testing in Ensuring Batch Consistency
Even when sourcing high-quality materials, variations can occur between batches. This is where material testing becomes crucial. Before entering the production line, each batch of material can be tested for properties like hardness, elasticity, and chemical composition. Such tests ensure that the material aligns with the expected standards and that any deviations can be addressed before they impact the production process.
Addressing Challenges Posed by Different Metals and Alloys
Different metals and alloys come with their own sets of challenges. For example, while aluminum might be prized for its light weight and malleability, it can also be more prone to warping under high temperatures compared to steel. On the other hand, harder metals like titanium, while offering exceptional strength, might require more force during the stamping process, potentially affecting the tooling’s lifespan.
To maintain precision, it’s essential to understand these challenges and adapt the stamping process accordingly. This might involve adjusting machine settings, using specialized tooling, or even altering the design to accommodate the material’s properties.

The Influence of Tooling Design on Precision
In the realm of high-volume metal stamping, the machinery and materials used are undeniably crucial. However, the tooling – the dies and molds that shape the metal – plays an equally pivotal role in ensuring precision. The design and maintenance of these tools can significantly influence the accuracy and consistency of the stamped components.
Designing Tools for Repeatability and Minimal Wear
A well-designed tool is one that can consistently produce the same result, batch after batch. This repeatability is a cornerstone of precision in metal stamping. To achieve this, tools must be designed with materials and geometries that resist wear, even under the immense pressures and frictions of the stamping process. Furthermore, the tool’s design should facilitate even distribution of force, ensuring that the metal is shaped uniformly every time.
The Significance of Regular Tool Inspections and Replacements
Even the best-designed tools will wear down over time, especially in high-volume operations. As they wear, the precision of the stamping can begin to drift. Regular inspections can catch signs of wear before they impact product quality. By measuring tool dimensions, checking for signs of damage, and even using technologies like laser scanning, manufacturers can determine when a tool is nearing the end of its useful life. Timely replacements or repairs can then be made, ensuring uninterrupted precision.
Innovations in Tooling Materials and Design for Enhanced Lifespan
The world of metal stamping is not static. As challenges arise, innovations follow. New materials, such as tungsten carbide or advanced ceramics, are being explored for their potential to extend tool lifespans. These materials can resist wear better than traditional tool steels, especially in demanding applications.
Additionally, advances in design methodologies, aided by computer simulations, are allowing for the creation of tools that optimize force distribution, reduce stress points, and enhance overall durability. Such innovations not only extend the life of the tools but also ensure consistent precision throughout that life.

Case Studies: Success Stories in High-Volume Precision Stamping
The journey to mastering precision in high-volume metal stamping is paved with challenges, innovations, and continuous improvements. Several industries have set benchmarks in this domain, showcasing how precision can be maintained even when producing components in large volumes. Let’s delve into some success stories from various sectors.
How Automotive Giants Achieve Precision in Mass-Produced Components
The automotive industry, with its massive demand for stamped components, stands as a testament to high-volume precision stamping. Companies like Toyota and Volkswagen have implemented the Toyota Production System and Lean Manufacturing principles, respectively. These methodologies emphasize waste reduction, continuous improvement, and meticulous quality control. For instance, Toyota’s “andon” system allows any worker to halt the production line if a defect is detected, ensuring that only precise components move forward in the production process. Such stringent quality checks, combined with state-of-the-art machinery, ensure that millions of car parts are stamped with consistent precision.
Lessons from the Electronics Industry: Stamping Miniature Components with Precision
The electronics industry, particularly in the realm of smartphones and microchips, requires the stamping of incredibly small and intricate components. Companies like Apple and Samsung have mastered the art of producing these tiny parts with impeccable precision. Advanced micro-stamping techniques, combined with rigorous quality control measures, ensure that every tiny connector, pin, or chip holder is stamped to exact specifications. The success of these companies in maintaining precision in such miniature components underscores the importance of innovation and quality control in high-volume stamping.
Aerospace Industry Benchmarks in High-Volume Precision Stamping
The aerospace sector, where even the slightest deviation can have grave consequences, has set high benchmarks in precision stamping. Companies like Boeing and Airbus source stamped components that must adhere to strict international aerospace quality standards. These components undergo rigorous testing, from tensile strength assessments to thermal simulations, ensuring they meet the exacting standards of the aerospace industry. The success of these aerospace giants in maintaining precision, even in high-volume production runs, highlights the importance of stringent quality standards and rigorous testing protocols.
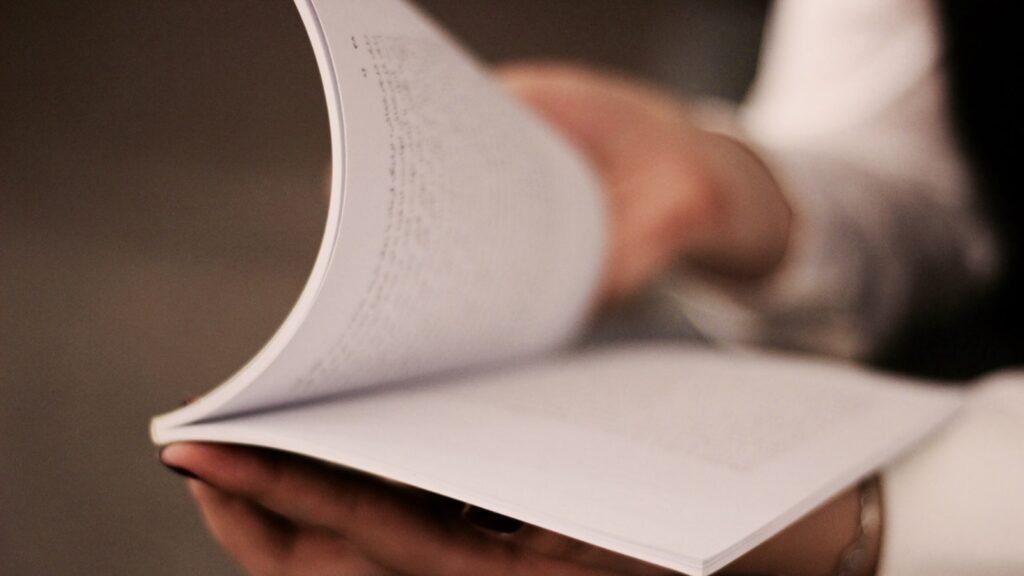
Embracing Technological Advancements for Enhanced Precision
In the ever-evolving world of manufacturing, staying ahead of the curve is crucial, especially when precision is paramount. The integration of cutting-edge technologies has revolutionized the way high-volume metal stamping is approached, ensuring even greater accuracy and efficiency. Let’s explore some of these technological advancements and their impact on precision.
Role of AI and Machine Learning in Predictive Maintenance
Artificial Intelligence (AI) and Machine Learning (ML) have made significant inroads into the manufacturing sector, particularly in predictive maintenance. By analyzing vast amounts of data from stamping machines, AI algorithms can predict when a machine is likely to fail or when a tool might wear out. This proactive approach ensures that maintenance can be scheduled before a breakdown occurs, minimizing downtime and ensuring consistent precision. Moreover, ML models can learn from past defects and inefficiencies, continuously improving the stamping process over time.
The Future of Robotics in High-Volume Metal Stamping
Robots, with their ability to work tirelessly and with consistent accuracy, are becoming indispensable in the metal stamping industry. Advanced robotic arms equipped with sensors can handle intricate stamping tasks with a level of precision hard for humans to match. As these robots become more sophisticated, they can adapt to changes in the stamping process in real-time, ensuring that precision is maintained even in high-volume runs. Furthermore, collaborative robots, or “cobots,” are designed to work alongside humans, combining the strengths of both to achieve unparalleled precision.
How Digital Twins and Simulations Aid in Achieving Precision
The concept of a “digital twin” – a virtual replica of a physical product, process, or system – has gained traction in the manufacturing world. In the context of metal stamping, digital twins can simulate the entire stamping process, allowing manufacturers to identify potential issues before they arise in the real world. By tweaking the simulation, they can optimize the stamping process for maximum precision. Additionally, real-time simulations can provide feedback during the stamping process, allowing for on-the-fly adjustments to maintain accuracy.

Conclusion
Maintaining precision in high-volume metal stamping is a multifaceted challenge that requires a blend of advanced technology, skilled workforce, and stringent quality control measures. As the industry evolves, embracing these best practices will be the key to achieving unparalleled precision, irrespective of the production volume.
