When it comes to selecting the right type of steel for your project, the myriad of options available can be overwhelming. Among the contenders, galvanized and galvannealed steel are often at the forefront due to their enhanced corrosion resistance. However, despite the similar names, these materials serve different purposes and exhibit distinct characteristics. This post will unravel the essential differences between galvanized and galvannealed steel, guiding you in making an informed decision based on your project requirements.
Galvanized steel is a type of steel that has been coated with a layer of zinc to protect it from corrosion, whereas galvannealed steel undergoes an additional annealing process after galvanizing to enhance its paint adhesion and weldability. While galvanized steel offers better corrosion resistance, galvannealed steel provides better paintability and weldability, making each suitable for different applications.
As we delve deeper, we’ll explore the manufacturing processes of galvanized and galvannealed steel, their benefits, and common applications. Moreover, we’ll provide a comparative analysis of their performance attributes, cost considerations, and industry preferences. This comprehensive discussion will equip you with the knowledge needed to select the ideal steel type for your project, ensuring durability, cost-effectiveness, and operational efficiency. So, whether you’re in the automotive sector or construction, understanding the core differences between galvanized and galvannealed steel is paramount in achieving the desired outcome for your endeavors.
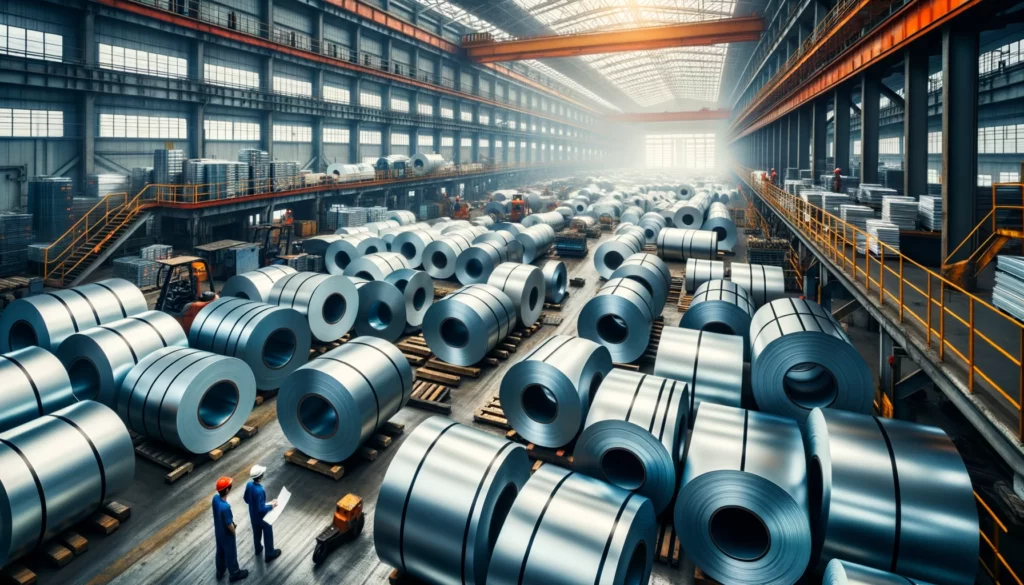
Understanding Galvanized Steel
Galvanized steel is a type of steel that has undergone a process to prevent it from corroding by applying a protective zinc coating. This is achieved through a process known as hot-dip galvanizing, where the steel is submerged in a molten zinc bath. The zinc reacts with the steel, forming a tightly-bonded alloy coating that serves as a robust barrier against corrosive elements such as moisture and salt.
Benefits:
- Corrosion Resistance: The primary benefit of galvanized steel is its resistance to corrosion, which significantly extends the material’s lifespan. This is particularly advantageous in outdoor or harsh environments where exposure to elements would otherwise lead to rapid degradation of the metal.
- Cost-Efficiency: Galvanized steel is generally more cost-effective compared to other corrosion-resistant materials. The galvanization process is less expensive, and the resulting product requires less maintenance, thereby reducing long-term costs.
- Durability: The zinc coating provides a hard, scratch-resistant surface, enhancing the durability of the steel. This is essential in applications where the material will be subject to physical stress or heavy wear.
- Recyclability: Galvanized steel is fully recyclable without loss of quality, aligning with sustainability goals of many projects and companies.
Common Applications:
Galvanized steel finds a broad spectrum of applications across various industries due to its corrosion resistance and durability. Some of the common applications include:
- Construction: It’s widely used in structural applications, roofing, wall cladding, and decking.
- Automotive: Used in body structures, chassis, and various other components to ensure longevity.
- Infrastructure: Utilized in bridges, highways, and in making poles, signs, and guardrails.
- Agriculture: Employed in making farm machinery, storage, and protective enclosures.
- Industrial: Galvanized steel is used in manufacturing machinery, equipment, and other industrial appliances.
The versatility, combined with the robust protective attributes of galvanized steel, makes it a preferred choice in projects aiming for long-term stability and minimal maintenance.
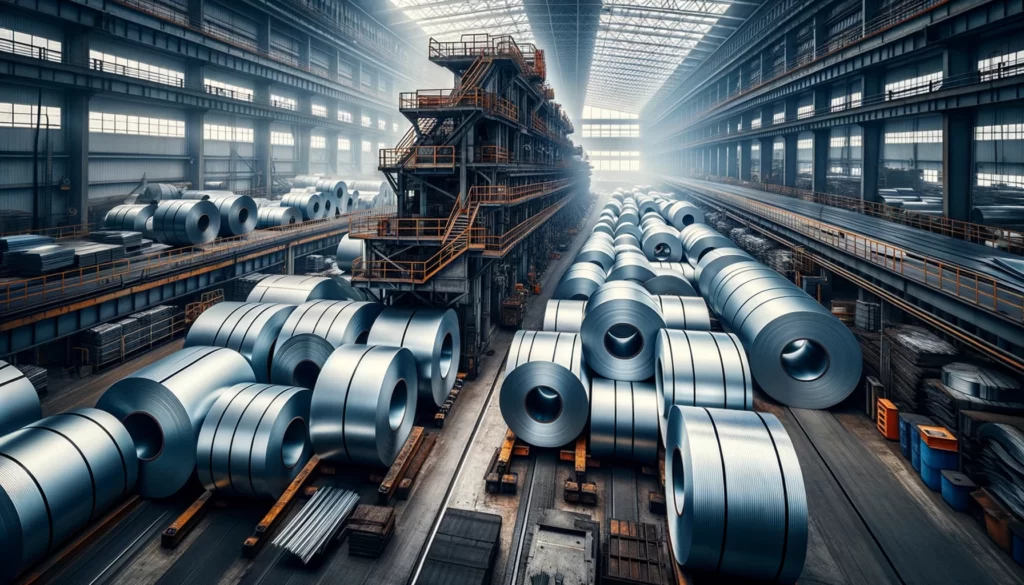
Unveiling Galvannealed Steel
Galvannealed steel is a result of a dual process which involves galvanizing and annealing. Initially, the steel is hot-dip galvanized, but then, it undergoes an additional annealing process. During the annealing process, the zinc coating is diffused into the steel, creating a zinc-iron alloy surface. This alloy surface is harder than a standard galvanized coating, and it’s more suitable for painting.
Benefits:
- Paint Adhesion: The primary advantage of galvannealed steel over galvanized steel is its surface’s ability to retain paint. The zinc-iron alloy surface provides a better bonding surface for paint, eliminating the need for a primer. This characteristic is vital in applications where aesthetics or additional protection is required.
- Corrosion Resistance: While it may not offer as much corrosion resistance as galvanized steel, galvannealed steel still holds up well against rust, especially when painted.
- Formability: The zinc-iron alloy coating is softer and more ductile than a purely zinc coating. This attribute facilitates easier forming and bending of the steel, making it a suitable choice for intricate parts or complex shapes.
- Weldability: Galvannealed steel is better suited for welding applications compared to galvanized steel due to the zinc-iron alloy coating.
Common Applications:
Due to its unique set of benefits, galvannealed steel finds utility in a variety of sectors and applications:
- Automotive Industry: It’s widely used for body panels and other parts that require good paintability and formability.
- Construction: Employed in architectural and structural elements where the steel needs to be formed into shapes while retaining corrosion resistance.
- Electrical Enclosures: The ability to paint galvannealed steel makes it a popular choice for electrical enclosures and cabinets.
- Home Appliances: Used in the manufacturing of appliances like washers, dryers, and ovens due to its paintable surface.
- Heating and Cooling Systems: Utilized in making ducts and other components of HVAC systems.
Galvannealed steel’s blend of paintability, formability, and moderate corrosion resistance makes it a versatile material, bridging the gap between aesthetics, durability, and workability.

Core Differences Between Galvanized and Galvannealed Steel
The distinction between galvanized and galvannealed steel stems from the processes used to treat them, which in turn influence their performance attributes. Here’s a detailed look into their differences:
Process Comparison: Galvanizing vs. Galvannealing
- Galvanizing: This process involves immersing steel in a molten zinc bath, coating it with a layer of zinc to protect it from corrosion. The zinc acts as a sacrificial anode, corroding in place of the steel and providing a physical barrier to environmental factors.
- Galvannealing: Galvannealing starts with the same hot-dip galvanizing process, but it doesn’t end there. Post galvanizing, the steel is heated further in an annealing furnace, allowing the zinc to alloy with the iron molecules within the steel, forming a zinc-iron outer layer.
Performance Attributes
- Corrosion Resistance:
- Galvanized Steel: It offers superior corrosion resistance due to the thicker, pure zinc coating.
- Galvannealed Steel: Although corrosion-resistant, it doesn’t quite match the level of galvanized steel. However, once painted, its corrosion resistance significantly improves.
- Paintability:
- Galvanized Steel: The smooth zinc coating can make adhesion more challenging; it usually requires a primer to ensure paint adhesion.
- Galvannealed Steel: Its rougher, zinc-iron alloy surface is more conducive to paint adhesion without the need for a primer.
- Weldability:
- Galvanized Steel: Welding can be problematic due to the zinc coating, which can create harmful fumes and leave a less desirable weld appearance.
- Galvannealed Steel: With its zinc-iron alloy coating, galvannealed steel is easier to weld, and harmful fumes are less of a concern.
- Formability:
- Galvanized Steel: Its coating can crack during forming, which might expose the steel to corrosion.
- Galvannealed Steel: The alloy coating is more ductile, allowing for better formability without cracking.
- Cost:
- Galvanized Steel: Generally, it might be more cost-effective due to a simpler process.
- Galvannealed Steel: The additional annealing process may add to the cost.
The choice between galvanized and galvannealed steel largely depends on the application’s requirements. While galvanized steel stands out for its superior corrosion resistance, galvannealed steel, with its better paintability and weldability, might be the preferred choice for automotive or manufacturing projects where painting or welding are essential steps.

Making the Right Choice: Galvanized or Galvannealed?
Selecting between galvanized and galvannealed steel is not a one-size-fits-all decision but hinges on several factors related to your specific project. Here are some key considerations to guide you in making an informed choice:
Project Requirements Assessment
- Environment: If the steel will be exposed to harsh environmental conditions, galvanized steel with its superior corrosion resistance would be a better choice. On the other hand, if paintability is a priority, galvannealed steel is more apt.
- Welding Needs: For projects requiring extensive welding, galvannealed steel is a more suitable option due to its better weldability compared to galvanized steel.
- Forming Operations: If your project involves a lot of forming operations, the ductility of galvannealed steel might prove beneficial as it reduces the risk of coating cracking.
Cost Considerations
- Initial Costs: Galvanized steel might have lower initial costs due to a simpler manufacturing process. However, if your project requires a primer for painting or additional welding preparations, these costs could add up.
- Long-term Costs: Galvannealed steel, with its better paint adherence and weldability, might save costs in the long run, especially if it reduces the need for secondary operations or maintenance.
Durability and Maintenance
- Maintenance Needs: Galvanized steel might require less maintenance in corrosive environments, while galvannealed steel might fare better with painted applications.
- Lifespan: Both materials are durable, but the choice that aligns with your project needs will likely have a longer lifespan in the given application. For instance, the corrosion resistance of galvanized steel might translate to a longer lifespan in outdoor or marine environments.
Final Verdict
The decision boils down to your project’s unique requirements and the conditions the final product will be subjected to. It’s advisable to consult with metal fabrication experts or the steel suppliers to ensure that the choice of steel aligns with the project goals, ensuring optimal performance, durability, and cost-effectiveness in the long run.
Industry Preferences: A Look at Trends
The choice between galvanized and galvannealed steel often aligns with the demands of specific industries and the evolving trends therein. Let’s explore the adoption trends in some key sectors along with recent advancements in steel coating processes that might influence these preferences.
Adoption Trends in Automotive, Construction, and Other Sectors
- Automotive: The automotive sector often leans towards galvannealed steel due to its superior paintability and weldability, crucial for both aesthetic and structural elements of vehicles. However, galvanized steel is also utilized for its corrosion resistance, especially in underbody applications.
- Construction: In construction, the preference is generally skewed towards galvanized steel owing to its robustness against environmental adversities. Its resistance to corrosion makes it a go-to choice for structural components exposed to the elements.
- Appliances and HVAC: Galvannealed steel, with its fine finish and paint adherence, finds favor in the manufacturing of appliances and HVAC systems, where aesthetics and functionality are pivotal.
Recent Technological Advancements in Steel Coating Processes
- Advanced Coating Techniques: Innovations like high-grade zinc coatings and passivation processes have further enhanced the corrosion resistance of galvanized steel, making it even more appealing for outdoor applications.
- Improved Annealing Processes: Advancements in annealing processes have augmented the quality of galvannealed steel, improving its surface finish and paint adherence, which is vital for industries where aesthetic appeal is a priority.
- Eco-friendly Coating Solutions: The push towards environmentally friendly solutions has led to the development of organic coatings and other eco-conscious treatments that enhance the properties of both galvanized and galvannealed steel, aligning with the sustainability goals of modern industries.
These trends and advancements not only reflect the growing sophistication in steel coating technologies but also the industry’s ongoing quest for materials that strike a balance between performance, cost-efficiency, and environmental responsibility. The continuous evolution in coating processes is likely to further refine the advantages of galvanized and galvannealed steel, catering to the nuanced needs of different industrial domains.

Conclusion
In sum, the choice between galvanized and galvannealed steel hinges on the specific requirements of your project. Galvanized steel stands out for its corrosion resistance and is apt for outdoor constructions, while galvannealed steel, with its better paintability and weldability, is well-suited for automotive and aesthetic applications. Assessing the cost, durability, and the operational environment will guide you in making an informed decision tailored to your project’s needs.